Delving into the realm of commercial construction, one encounters a variety of classifications designed to ensure safety, functionality, and longevity of structures. Among these is Type C construction, a classification that prioritizes the use of non-combustible materials and maintains strict compliance with fire resistance standards.
Understanding these classifications can be crucial for anyone involved in designing, planning, or constructing commercial buildings. This article provides a detailed look at what defines Type C construction, its requirements, and how it impacts both the construction process and the finished project. So, whether you're an aspiring architect, a seasoned developer, or just curious about building standards, let's explore what makes Type C construction uniquely essential in commercial projects.
- Introduction to Type C Construction
- Regulatory Framework and Compliance
- Materials and Structural Components
- Fire Safety and Resistance Considerations
- Cost Implications and Budgeting
- Practical Applications in Commercial Projects
Introduction to Type C Construction
When navigating the complex world of commercial building, encountering terms like Type C construction can initially strike you as a bit abstruse. Yet, the relevance of understanding such classifications is far from trivial. At its core, Type C construction stands for a specific category within the building codes, primarily dictated by its reliance on non-combustible materials. These materials ensure that structures are more resistant to fire, adding a layer of safety mandated by regulations such as the New Zealand Building Code or international equivalents.
Type C constructions are typically required to have certain fire-resistant features, though not as stringent as other types like A or B. This classification makes them suitable for various commercial structures that need safety without the cost of more rigid requirements. For example, buildings with lower occupancy loads or lower heights often fall into this category. A defining feature in the building world, the 'C' categorization involves using materials like reinforced concrete, steel, and other substances that can endure flames longer than wood or untreated materials. However, each project’s specifics, such as its location, intended use, and design aspects, might slightly tweak these requirements.
In this context, the evolving landscape of climate consciousness offers fertile ground for innovations that appeal to sustainable practices. This essence of progress is echoed in government regulations and initiatives. Recently, a quote from the Ministry of Business, Innovation, and Employment stated:
"Promoting the use of non-combustible materials not only ensures safety but aligns with our vision for environmentally sustainable practices in future construction."The commitment towards resilient infrastructure that marries safety and sustainability is not just a desirable path but a necessary journey for many stakeholders, including architects, planners, and lawmakers involved in commercial construction.
Interestingly, despite its cautious stance on fire safety, Type C constructions often offer a unique aesthetic versatility that appeals to modern commercial developers. The materials involved lend themselves to intriguing architectural designs that could cater to a variety of functions within a brilliantly designed structure. Whether considering a new office development or a multi-purpose shopping center, knowing the canvas Type C offers can help build intriguing plans that deftly marry function with form.
Regulatory Framework and Compliance
In the world of commercial construction, the regulatory framework governing Type C construction is both vital and intricate. These regulations ensure that buildings meet specific safety and structural integrity standards, which are crucial for protecting both property and human lives. The basis of these frameworks is often rooted in building codes, which are a set of guidelines that dictate everything from the types of materials allowed to the specific fire resistance ratings required for various structural elements. In New Zealand, for instance, the NZ Building Code is a significant legislative document that builders and developers must comply with. The code emphasizes the importance of fire safety, stipulating that certain materials classified as non-combustible must be used in specific situations.
Understanding these codes involves not just knowing the materials but also the tests and certifications these materials have undergone. For Type C construction, compliance with fire resistance standards is critical. It's not just about ensuring that materials won't combust, but also about guaranteeing that, in the event of a fire, structural components can withstand heat for a designated period. This aspect of compliance requires rigorous testing and certification processes, often conducted by independent testing agencies. These agencies use standardized methods to evaluate the fire resistance of materials, and their results provide a basis for compliance with regional building codes. In making these assessments, recognized international standards such as those from ASTM International or the International Organization for Standardization (ISO) might be used to ensure a level of consistency and reliability in testing.
The construction industry must also keep an eye on amendments in these regulations, as they can evolve due to changes in technology, climate considerations, or after significant fire events. Australia's National Construction Code (NCC), for example, undergoes regular updates to reflect new insights and strategies in building safety.
The significance of staying up-to-date is highlighted by Tim Thompson, a noted civil engineer, "Building codes are not static; they evolve as our understanding of safety and technologies improve. Compliance isn’t just about meeting current standards; it's about anticipating and preparing for future ones."These updates mean that both contractors and designers need to actively engage with professional communities and regulatory bodies to remain compliant.
Beyond the legal requirements, meeting the regulatory standards for Type C construction can also have profound impacts on project timelines and budgets. Fulfilling the criteria set forth in the codes requires meticulous planning and expertise in both material selection and architectural planning. Companies might need to engage specialists like fire engineers or compliance consultants to navigate these requirements effectively. This involvement can add to the project cost but ensures that the risk of compliance failure, which could lead to expensive retrofits or insurance complications down the line, is minimized. Ultimately, understanding and adhering to these regulatory frameworks represents not just a statutory hurdle but a commitment to quality and safety in every commercial construction project.
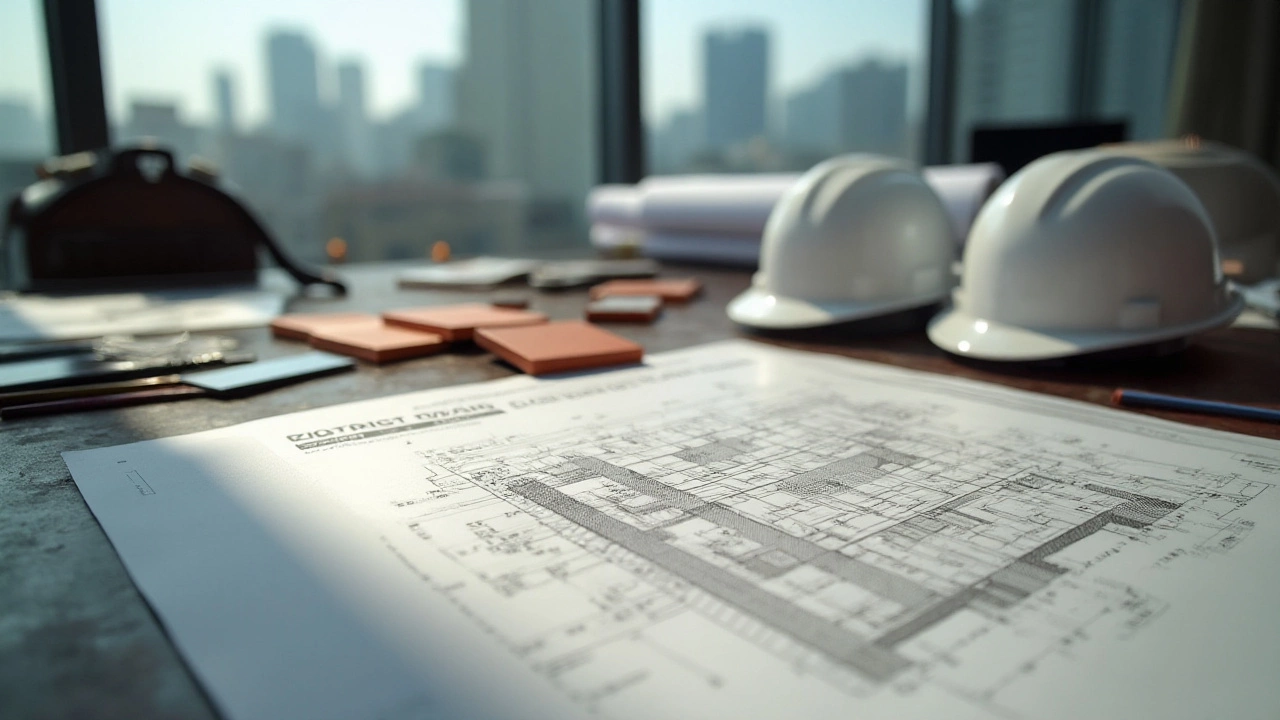
Materials and Structural Components
Type C construction is governed by a specific set of criteria detailing the use of materials and structural elements designed to ensure non-combustibility and fire resistance. These criteria are typically outlined in local building codes, which stipulate not only the types of materials that can be used but also how these materials should be applied throughout the construction process. The primary aim here is to minimize the potential spread of fire and provide vital time for evacuation and firefighting efforts. In this context, non-combustible materials play a pivotal role, often including concrete, steel, and certain metal alloys, which are known for their high heat resistance and structural integrity. Concrete, for instance, is particularly valued in Type C construction due to its robust fire-resistive properties and versatility in various applications.
When considering concrete as a primary component, it's vital to understand its behavior under extreme heat conditions. Concrete retains much of its strength at high temperatures, which is why it's frequently used in constructing floors, walls, and ceilings in commercial buildings that demand fire safety. In contrast, steel, another cornerstone of non-combustible construction, has both advantages and limitations. It's incredibly strong and flexible, allowing architects the freedom to design with more creativity, but it also loses strength rapidly when exposed to direct fire unless treated or coated with protective materials. Fireproofing methods, such as intumescent coatings that expand to form a protective barrier, are commonly employed to enhance the fire resistance of steel structures.
"Building fire-safe structures is not just about materials; it’s a combination of intelligent design and practical materials application," notes Marina Walsh, a leading figure in commercial construction safety research.
Beyond the basic non-combustible materials, Type C construction might also incorporate specialized glass and gypsum products designed to resist heat and mitigate fire spread. Fire-resistant glazed glass panels, for instance, are used to allow natural light into a space while maintaining strict fire boundaries. These panels are treated to withstand temperatures up to 1,000 degrees Celsius, providing extra time for building occupants to evacuate safely. Fire-rated gypsum boards are another essential component, usually implemented as part of the interior finishing systems, enhancing the overall fire resistance rating of floors, walls, and partitions.
Moreover, for effective commercial building projects, one must consider how these materials are combined to create a structure that not only meets regulatory requirements but also achieves aesthetic and functional objectives. Architects often use these materials creatively to construct engaging and inviting spaces without compromising on safety. It's also worth noting that while initial costs for these materials may be higher than less fire-resistant alternatives, the long-term benefits of increased safety and potential insurance savings can make Type C construction an economical choice.
The integration of non-combustible materials goes beyond mere selection; it's about using them in a way that contributes to a building's total fire protection strategy. Inspections and the consideration of load-bearing capabilities under fire conditions are critical in maintaining structural stability. As such, engineers and architects alike must work closely to assess and implement systems that maximize the potential of each material, using advanced modeling tools to simulate fire scenarios and optimize design. This collaborative approach ensures that Type C constructions not only comply with current codes but are also resilient enough to meet future challenges posed by urban expansion and evolving safety standards.
Examples of Material Applications
Several modern commercial projects worldwide exemplify the innovative application of materials specific to Type C construction. For example, in urban office blocks, where steel frames form the skeleton of skyscrapers, integrating fire-resistant materials and technologies has evolved into an art. In recent years, composite floor decks—combining reinforced concrete with fire-protected steel—have become the staple of high-rise construction. This blend optimizes both performance and cost, offering enhanced resilience and swift construction timelines. As cities talk of smart buildings, these practices highlight a balance between innovation and compliance that defines the frontier of commercial construction.
Fire Safety and Resistance Considerations
When it comes to ensuring the safety and longevity of commercial buildings, Type C construction plays a pivotal role in embedding essential fire safety measures into the structure. At the heart of these considerations is the commitment to using non-combustible materials, such as steel and concrete, which inherently resist fire better than their wooden counterparts. These materials are not only crucial in slowing the spread of fire but also in maintaining the structural integrity of the building under high-temperature conditions. This is more than a mere safety protocol; it's a systematic approach to protecting both assets and lives. In fact, building codes often stipulate specific fire resistance ratings that must be met, ensuring that the materials used can withstand fire for a set duration under standard conditions.
It’s interesting to note that the importance of fire resistance in construction isn't a new concept. Historical records show that even the Romans understood the need for fire-resistant materials, using stone and tile to safeguard their monumental structures. This ancient wisdom is echoed in today’s strict building codes and regulations, where architects and builders work closely to meet or exceed the required standards. A key aspect of this process is the integration of detailed fire protection plans, which include fire stops, barriers, and fire-resistant coatings that enhance the protective attributes of the materials. These plans underscore the seriousness with which fire safety is treated in the industry. A failure to comply not only endangers lives but can lead to legal ramifications and financial losses for stakeholders.
The implementation of fire safety measures in commercial construction involves several technical and strategic aspects. Among these is the incorporation of advanced technologies like fire suppression systems and thermal barriers that provide an additional layer of protection. These systems are often automated and integrated with building management systems to ensure immediate response in case of a fire outbreak. The fire detection and alarm systems are also continuously evolving, with smart technologies providing more precise detection and faster emergency response capabilities. These advancements offer significant improvements over traditional systems, which could be less effective and sometimes even unreliable.
"Fire safety is not just a regulatory requirement; it’s a moral obligation to ensure the well-being of building occupants," says Emily Carter, a renowned architect specializing in sustainable urban developments.
This detailed approach to fire safety and resistance is not just about ticking boxes on a compliance checklist. It involves an understanding of the materials' chemical and physical properties, the way they interact in the event of a fire, and how best to utilize them within a building’s design. Structural elements like beams and columns are often treated or encased to enhance their resistance, reflecting an ongoing commitment to innovation in the field of commercial building safety.
To give you an idea of how fire resistance is quantified, let's look at the fire resistance requirements often specified in building codes. For instance, a table might designate that structural walls must have a resistance rating of two hours, meaning they can withstand fire exposure for that duration without collapsing. Floors and roofs may have a one-hour requirement. These ratings are established through rigorous testing under laboratory conditions, simulating both the heat and structural loads that a real fire would impose.
Building Component | Fire Resistance Rating |
---|---|
Structural Walls | 2 Hours |
Floors and Roofs | 1 Hour |
Building Partitions | 1 Hour |
Adhering to these guidelines not only helps prevent catastrophic losses during a fire but also protects the lives of occupants while preserving property. This extends the resilience and redundancy built into the structure, ensuring that even amidst unforeseen circumstances, the building stands strong, safeguarding all within. The emphasis on fire resistance in Type C construction reflects a broader industry trend towards comprehensive safety and risk mitigation strategies in modern commercial architecture.
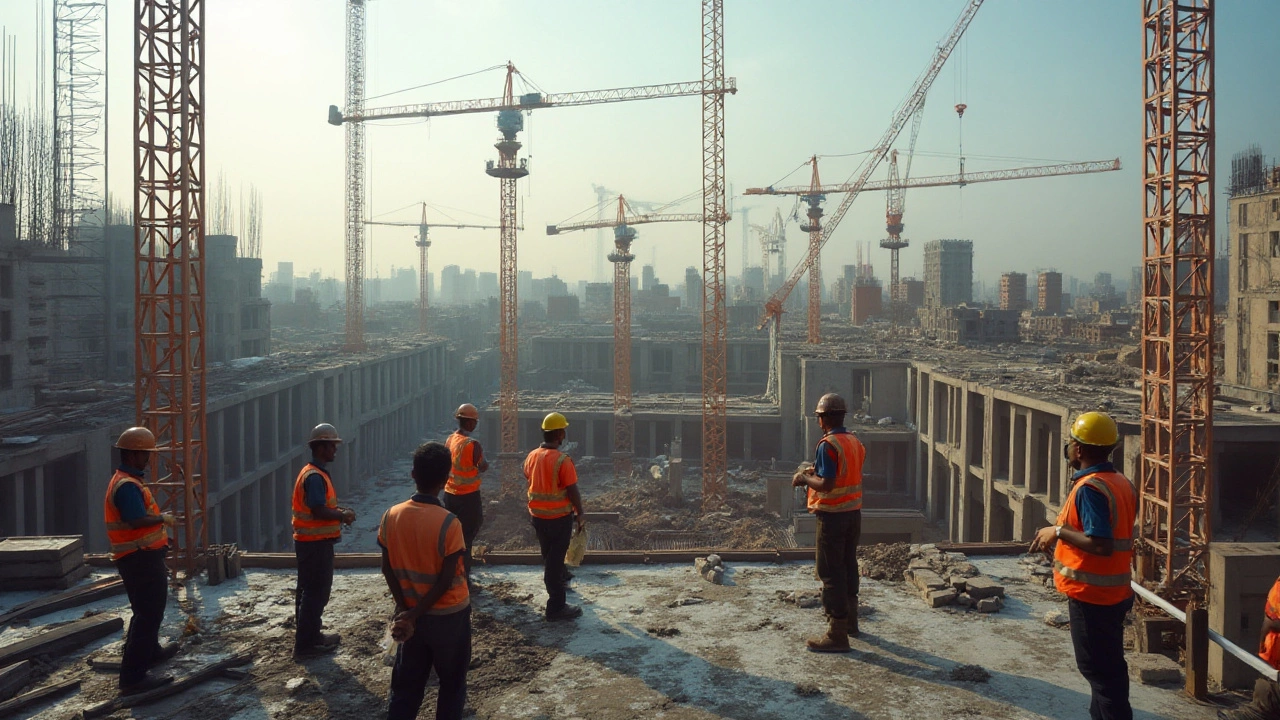
Cost Implications and Budgeting
When it comes to managing projects with Type C construction, understanding the financial aspect is pivotal. The cost implications of adopting this construction type can be significant, yet they often promise long-term benefits that outweigh the initial expense. The decision to use non-combustible materials, for instance, may come with a higher price tag compared to traditional options. Steel and concrete, common choices in Type C construction, are known for their durability and fire-resistance capabilities. These materials demand an upfront investment, but they contribute to lower maintenance costs over the building's lifespan, providing a balance of safety and economy.
Budget considerations in such projects aren't solely about material costs. Labor costs might also see a shift due to the technical expertise required in handling specific materials or adhering to stricter compliance standards. Balancing these aspects requires foresight and knowledge, often turning budgeting into a sophisticated art. Contractors and project managers must factor in potential contingencies, supply chain disruptions, and the ever-evolving nature of building regulations. A comprehensive budget plan might integrate these variables, providing a buffer for unexpected scenarios, thus maintaining financial stability throughout the construction process.
One seasoned architect aptly noted, "The foundational investment in Type C construction not only manifests in the structural integrity but in the confidence of ensuring regulatory compliance and peace of mind," highlighting the dual benefit of cost and safety assurance. It's worth noting that regulatory bodies might offer incentives or subsidies for projects meeting high safety standards, which can be a silver lining for investors wary of the initial expenditures.
For stakeholders, crafting a budget plan requires meticulous analysis and realistic forecasting. The right blend of stringent cost controls and strategic financial allowances is essential in preventing budget overruns. Regular financial audits and updates can highlight areas in need of fiscal adjustment, ensuring the project adheres to its financial blueprint. By strategically planning for both expected and unforeseen expenses, developers can navigate the complexities inherent in this commercial construction method, harnessing potential savings and optimizing resource allocation.
Understanding these cost dynamics doesn't merely make a project feasible; it makes it sustainably profitable. Valuation exercises can illuminate prospective financial paths, highlighting sections of the project where alternative materials or methods might provide cost-efficiency without compromising the core benefits of Type C construction. In this manner, stakeholders are empowered to make informed decisions, balancing quality and fiscal responsibility, and curating a pathway that aligns with both their vision and financial capacity.
Practical Applications in Commercial Projects
When it comes to type C construction, one of the key factors driving its widespread adoption in commercial sectors is the blend of safety and economic feasibility. Imagine walking into a sprawling shopping mall or a tech-savvy office building; the likelihood is that the underlying structure is designed with Type C principles. These buildings utilize non-combustible materials predominantly, such as concrete, steel, and glass, ensuring both durability and strength while meeting essential fire resistance criteria. The emphasis on fire safety is not just a regulatory compulsion but a strategic choice, mitigating risks substantially and often positioning the project as a more attractive venture for investors.
Intriguingly, statistics reveal that buildings constructed under Type C guidelines often perform 20% better in fire endurance compared to lesser classifications. This has driven industries to lean on Type C for projects expecting high footfall or housing critical infrastructure. Consider, for instance, the design of data centers — these buildings absolutely cannot afford disruptions, hence the backing of a solid Type C framework serves as the backbone of their operational security.
Beyond just office spaces and centers of commerce, Type C construction is increasingly prevalent in multifunctional arenas and transport hubs. Airports, for instance, leverage this construction type not only because of the fire safety standards but due to the necessity for the buildings to withstand the vigors of constant human activity and mechanical operations. In the case of the Monaco International Airport, architect Pierre-Michel's team achieved an amalgam of aesthetic appeal and structural integrity by integrating innovative Type C materials, a move praised broadly across architectural forums.
It's worth noting that building classification also influences urban planning; cities aiming to bolster their green credentials and eco-friendly ratings consider Type C construction due to its sustainability potential. These projects often incorporate recycling efforts, using pre-existing materials wherever possible, which dovetails with governmental incentives in many regions. A quote from renowned architect Charles Landry expresses this perfectly:
"The choices we make in urban planning today, especially with non-combustible infrastructures, will be the green highways of tomorrow's cities."
In integrating type C construction into a project, several steps must be considered. Initially, it's crucial to consult with seasoned engineers and architects familiar with the nuances of this classification. Creating a blueprint that emphasizes both safety and functionality while harnessing the benefits of non-combustible materials can be a game-changer. A strategic planning phase should also thoroughly explore material sourcing, which might encompass regionally available products that align with the environmental aspirations of the community.
The diverse applications of Type C construction in commercial projects continue to evolve, with innovations pushing boundaries every year. Whether you're involved in a large-scale commercial build or a budding entrepreneur in the construction industry, understanding and applying Type C classifications can yield rewarding outcomes both for your business and the community it serves.
Write a comment