Forget what you know about expensive bricks and hefty labor bills—building a home doesn’t have to eat up your savings. With more people looking for budget-friendly ways to put a roof over their heads, the old-school idea that you need a massive loan or years of savings is flat-out wrong. It’s possible to build a house for much less than you might imagine, if you know which methods cut the cost without cutting corners on comfort or safety. The hunt for the cheapest building method isn’t new, but the tools, tricks, and materials continue to change. Why pay more for tradition when a smarter, leaner approach can keep more cash in your pocket?
What Makes a Building Method "Cheap"? Breaking Down the True Costs
Figuring out the cheapest way to build a house means looking past just the sticker price of materials. The real cost of building is a stew of materials, labor, speed, durability, and even what the local rules let you do. Some folks are shocked to learn that, depending on where you are, city fees and inspections might eat as much into your budget as concrete or lumber. That’s the first tip: local rules matter—always check them before you even dream up your plans. If a method is dirt cheap but not allowed, that's money down the drain.
Material costs are only the starting line. Bricks, wood, steel, or straw bales can all price out wildly different in 2025 depending on your location and even the month. Right now, lumber prices have cooled a bit from the pandemic surge, but concrete blocks can still jump up in cost if there’s a local supply bottleneck. Here’s a curious fact: in some U.S. states, you can cut costs nearly in half just by shifting from brand-new materials to using reclaimed wood or scrap metal. In practice, that means scouting salvage yards, Craigslist, or even demolition sites for reusable beams, windows, or doors can save thousands and adds a unique character to your project.
Labor is a hidden beast. Even if materials are cheap, if you need a crew of skilled workers for weeks—or if the build is technical—you’ll quickly bleed cash. Self-building (sometimes called owner-building or sweat equity) is the sharpest weapon for slashing labor bills. If you’re handy with tools, or can rope in family and friends for some pizza, the money you save avoids hourly rates that average $45–$100 per hour for pros. Even if you need to hire out the trickier parts (like electrical wiring, which should be done by a licensed contractor), you’re still banking the difference on simpler jobs like painting, flooring, or basic framing.
Speed matters more than most people guess. The longer a build drags on, the more it costs. Modular home kits, prefab panels, and concrete pours that cure in days instead of weeks shave time off the process, saving cash on everything from site rental fees to crew lunches. According to NAHB data from 2024, a stick-built house averages 7–9 months to finish, while a modular or prefab build wraps up in 2–4 months. That time saved is money in your pocket, not theirs.
Durability and lifespan also factor in. Say you pick the rock-bottom cheapest method—like earthen huts—but they need yearly repairs or struggle with the local climate. That’s not saving money, that’s deferring problems. A clever budget builder balances short-term savings with long-term expenses: it’s not cheap if you’re shoveling repair cash into a “savings” pit every season.
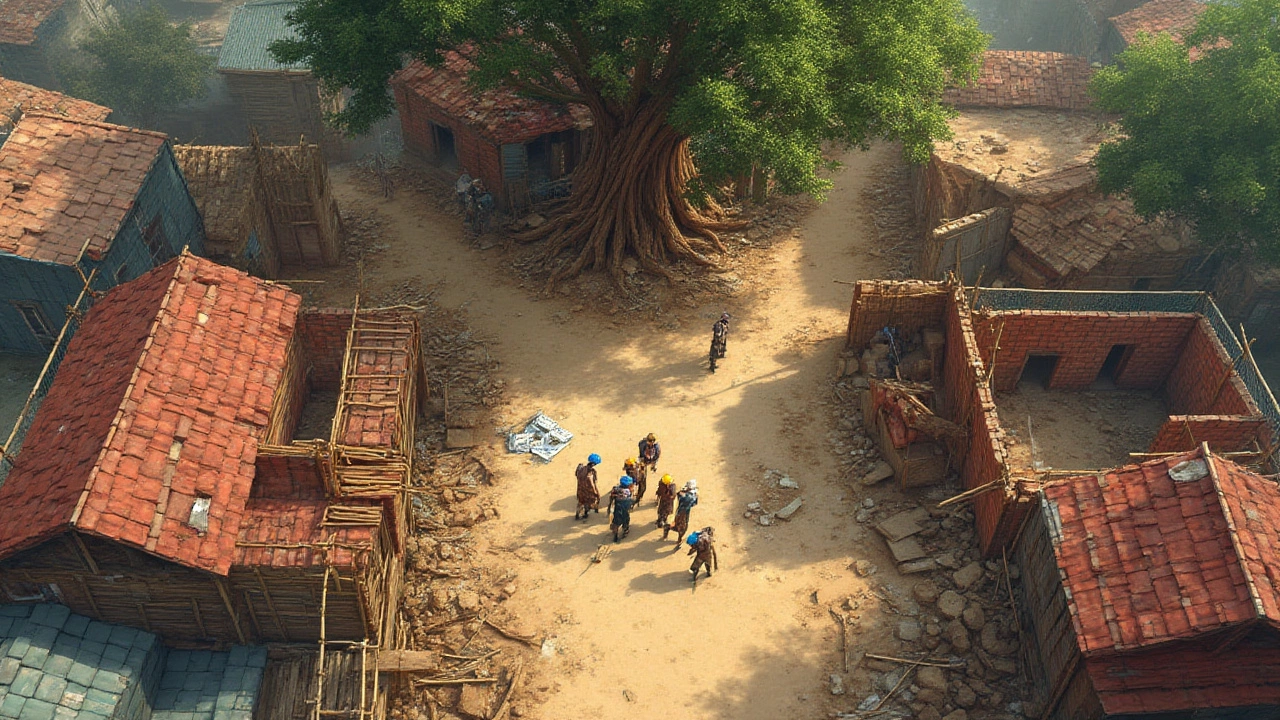
Top Low-Cost Building Methods in 2025: Pros, Cons, and Surprising Choices
The cheapest building method isn’t a one-size-fits-all answer. What works best in rural Texas might flop in frosty Michigan. Still, some methods stand out everywhere for raw affordability and how friendly they are to DIY efforts.
Let’s start with earthbag construction. This method looks as simple as it sounds: nylon or polypropylene bags are filled with dirt (sometimes mixed with a little sand or lime for stability), stacked into walls, then covered in plaster. It’s DIY gold—bags are cheap, dirt is often free, and the process doesn’t need heavy equipment. In warm, dry places like Arizona or New Mexico, earthbag homes hold cool air in summer and hold warmth in winter. There’s a growing movement of owners who knock out a 500-square-foot hut for under $15,000, all-in. Earthbags fit uneven land, odd shapes, and have survived magnitude-7 earthquakes when properly reinforced. Drawbacks? Let’s be honest: it’s not for everyone. Bag-filling is manual work, and not every city allows it. It’s also slow for bigger homes unless you have help.
Next on the low-cost list is straw bale building. Yes, it really uses bales of straw as the insulation and wall core, covered with plaster or stucco for weatherproofing. Straw is cheap, renewable, and (in dry areas) holds up well for decades. The insulation numbers are crazy good—R-values up to 28—so you save on heating and cooling forever. A typical straw bale house in the Midwest comes out 20–30% cheaper than the wood equivalent, even before you factor energy savings. But: straw bales can rot if not protected from rain, and they attract mice if not sealed well. This method does best in climates with low rainfall and needs careful foundations to avoid moisture climbing into the walls.
Shipping container homes are the rebels of affordable housing—turning old metal boxes into trendy, tough homes. The cost per square foot drops especially if you snag used containers without paying for fancy refurbs. With the global logistics slowdown in 2024, surplus containers became dirt cheap for a while, especially in port towns. You can stack them, mix and match lengths, and cut out walls for open-plan living. Bonus: they’re fireproof and nearly burglar-proof. But converting a container isn’t always as cheap as DIY bloggers say—you have to cut holes with torches, insulate against condensation, and meet code for wiring and ventilation. Still, folks have finished surprisingly slick, code-compliant homes for under $50,000 all-in using two or three containers (plus some serious elbow grease).
Don’t forget modular and prefab homes. Companies crank out entire houses in factories, then truck the pieces to your site to lock together in days. This takes advantage of economies of scale—you’re not paying for wood or concrete by the retail bag, you’re getting bulk product. Waste is minimal and labor is slashed because everything fits together kit-style. A recent HUD survey from late 2024 put the average cost of a modular single-family home at about $70–$110 per square foot, compared to $150+ for conventional builds. The best part: modern prefab looks nothing like cheap mobile homes. It can be as slick or rustic as you like. The catch? You need clear road access to your site (forget it on gnarly backroads) and must pay for a foundation and utility hookups, which bumps up the total cost.
Rammed earth is one more wild card. Dirt is slammed down between forms (like a giant sandcastle with a wooden frame), then sealed and often stabilized with a splash of concrete, lime, or asphalt emulsion. This technique is ancient but making a comeback in hip eco-building circles. Costs are low if you have cheap labor or can DIY—again, you need lots of muscle or machinery. The finished walls are thick, gorgeous, and nearly fireproof. The cons? If you get a stretch of wet weather, site delays can multiply. Also, not every building inspector is familiar with the method, so plan on lots of paperwork.
There are smaller methods worth a look, too. Tiny homes on wheels often skip a full foundation and can use wood, metal, or even SIP panels (structural insulated panels) for super-fast builds. Cinder block construction remains dirt cheap in most southern U.S. states, especially if you do the block-laying yourself. Bamboo is almost free in some tropical climates (like Florida or Puerto Rico) and makes bouncy, flexible structures that shrug off earthquakes.
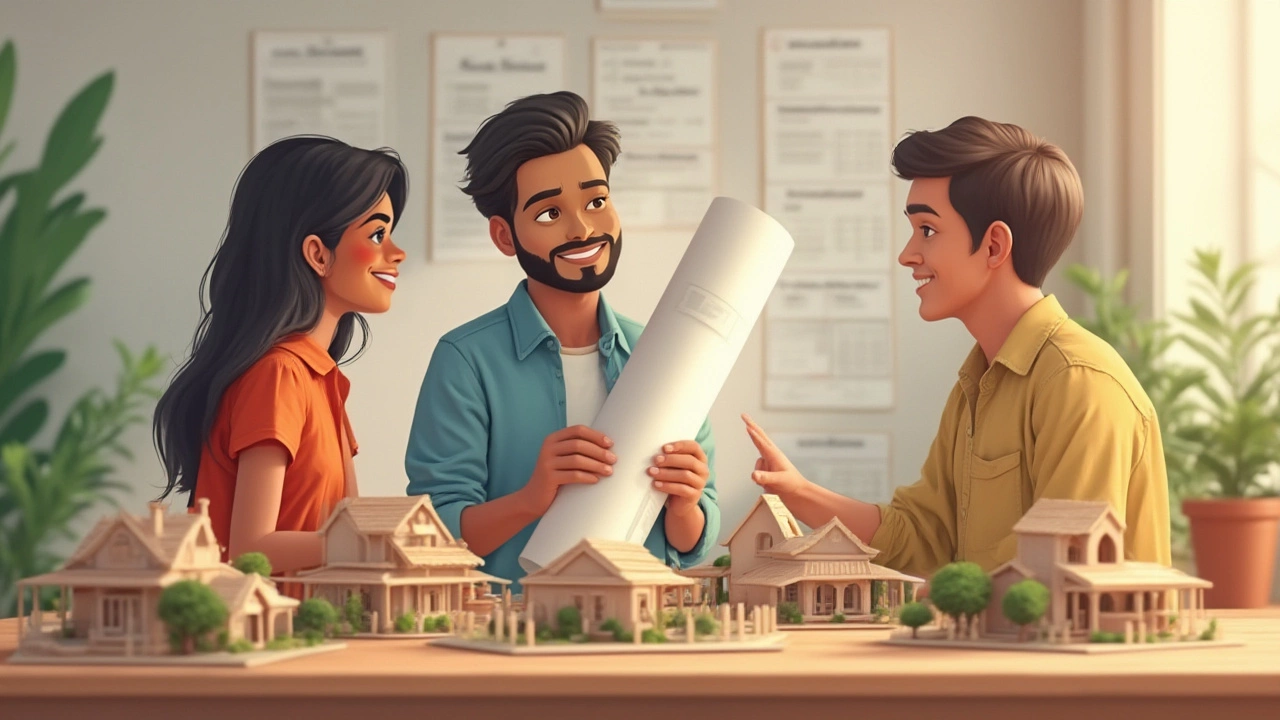
Smart Strategies to Build Even Cheaper: Tips That Actually Work
Saving money on building isn’t about pinching every penny until the house falls over. The cheapest building method combines sensible shortcuts, smart sourcing, and a willingness to rethink what "home" even means. Here are some proven ways to keep costs low, without sacrificing too much sanity or safety.
- Build small, but plan to expand. A tiny 400-square-foot starter home is way friendlier to your wallet than a sprawling 2,000-square-footer. Design for easy add-ons down the line if your budget improves. It’s not about living tiny forever, just starting affordably.
- Use reclaimed and salvaged materials when possible. Old barn wood, cast-off windows, Craigslist fixtures, and Habitat for Humanity ReStores are goldmines for budget builders. One Texas builder put up a whole 900-square-foot cabin with “trash” materials for under $8,000. Sometimes, all you need is a truck and a bold ask.
- Lock in price quotes for materials. In 2025, prices for concrete, plywood, and asphalt shingles are still jumpy. Negotiate with suppliers for a fixed price, or buy early and store onsite. Downtime hurts your budget, so don’t wait until the last minute for orders.
- Go off-grid where you can. City water and sewer hookups can cost more than a tiny house, especially in rural zones. If you’re willing to handle your own power, water catchment, or composting toilets, those savings can be redirected into better finishes or sturdier materials elsewhere.
- Barter labor or skills. Can you offer web design, car repair, or childcare in exchange for a friend’s expertise with framing or electrical? The days of trading services aren’t gone—they’re just waiting for creative folks to bring them back.
- Simplify the design. Shun complex floorplans, wild angles, and fussy rooflines. Every extra bump or corner means extra cuts, waste, and headaches. A plain rectangle with a simple pitched roof is the king of cheap, easy builds.
- Stay hands-on with permit paperwork. Hiring architects or "expediters" to wrangle the city can be expensive. Many homeowners tackle their own permit process after a little research—just double-check that your chosen method will fly with inspectors. Some counties even have separate, faster pathways for “alternative” construction methods.
- Don’t underestimate insulation. If you’re building with cheap but poorly insulating materials (like metal containers or thin boards), heat and cooling bills become monsters. Straw and SIPs cost a bit more upfront but chop electric bills for decades.
- Plan for resilience. Go too cheap and your house might not stand up to floods or windstorms. It’s better to spend $500 extra on hurricane strapping or reinforced foundations than rebuilding after the first season.
The very cheapest building method for you probably won't be the shiniest or the most mainstream. It’s a blend of what makes sense for your land, climate, skills, and how much help you can recruit. Some dream homes are built beside a woodshed, not a bank—it just takes a clear plan, a bit of research, and a whole lot of grit.
Write a comment